introduction
Fossil fuel-based thermal power plants are facing more problems as a result of rising energy demand and stricter environmental regulations. Some of the crucial components for its long-term success include clean combustion, emission reduction, and enhanced equipment efficiency. This calls for the creation of brand-new designs or the retrofitting of the current system with small adjustments to enhance system functionality and plant productivity. Power plants use CFD extensively in order to attain these goals with less expense and lead time while maintaining the quality of the outcomes. It is used to design and optimise as and Air passage system, including ducts, mixers, cyclone separators, dust collection systems, electrostatic precipitators, air preheaters, boilers, and boiler-related components like economizers and condensers, at a low cost.
Ducts
Any piece of machinery or procedure used in power plants and other process sectors will inevitably include ducting systems. It is crucial to design industrial ducts optimally to achieve a uniform flow pattern without increasing the pressure column in order to maximise plant productivity and cut back on auxiliary power use. Most power plants and industrial industries are adopting CFD as a common and affordable method to visualise the flow pattern.
Our expertise in these areas could assist you with
- Design optimisation of industrial ducts
- Analyzing and optimising flow patterns within ducts
- Analyzing the thermal load on ducts

Electrostatic Precipitator
An extremely demanding, dangerous, and corrosive environment is present for electrostatic precipitators used in power plants and the cement industry. To guarantee better construction and an effective operation that complies with pollution control standards, it has become extremely important to examine the flow characteristics of ESP inside the collection region and accompanying duct work. As a low-cost method and controlled environment for evaluating different design components, CFD is becoming increasingly important in the design evaluation and optimisation of ESPs. Through the use of CFD analysis, the time and money needed to carry out experimental activities for studying the flow unsteadiness, velocity stratification, flow angularity, and particulate deposition within an ESP might be minimized.
Our expertise in these areas could assist you with
- ESP system and associated duct flow pattern analysis
- ESP and associated duct flow process optimisation

Air Preheater Heating Element
In order to compare temperature, pressure, velocity, boundary heat transfer, turbulent kinetic energy, and nusselt number in detail, transient analysis of several Air Preheater Heating Element profiles was performed in a test setting. The most suitable heating element profile is chosen based on the results of the plant’s operating circumstances. The flow pattern is studied, and a uniform flow is established upstream of the Air Preheater using CFD analysis.
The velocity flow streamlines show the behavior of the flow and any potential stagnation zones. The turbulence properties of these zones are investigated, and steps are taken to reduce flow losses.

Combustion
Burning pulverised coal has a vital role in thermal power plants. It is ensured that the necessary heat transfer takes place to turn water into steam and prevent pollution when there is a sufficient supply of fuel and air for optimal combustion. Manufacturers of boilers and burners are facing new hurdles as a result of strict pollution emission rules, forcing them to either create brand-new, optimized boilers and burners or retrofit old systems with an optimal design. Power plants use CFD extensively to accomplish these design goals more quickly and at a lower cost. Any CFD analysis performed for power plants places a primary emphasis on predicting the flow of air and coal within the combustion chamber, the location of fire balls, the efficiency of nozzles and burners, the temperature of gas at crucial locations, and the reaction modelling of the combustion process.
Our expertise in these areas could assist you with
- Analysis and optimisation of industrial burners
- Analysis and optimisation of the boiler combustion chamber
- Flow pattern and temperature distribution of flue gases
Coal Combustion
In order to create heat, light, and gaseous byproducts, combustible elements in a fuel must quickly combine chemically with oxygen. Many of the byproducts produced during combustion are classified as pollutants and are dangerous to the environment, depleting the ozone layer and raising the temperature of the earth’s atmosphere, among other impacts. To eliminate the dangerous substances from the flue gas before it is released into the atmosphere, after-treatment systems must be put in place.
Due to the complexity of coal combustion, it is difficult to comprehend all of the characteristics of any type of coal’s combustion, including that of bituminous, anthracite, and lignite, as well as the systems design characteristics that affect combustion. This requires expensive experimental analysis. With the advent of contemporary computing power and the availability of simulation-based techniques like CFD, the aforementioned process of detailed assessment concerning combustion phenomena with regard to and resultant pollutant production can be done with little expense or experimental needs. To evaluate the combustion properties of various types of coal, devolatilization, char production, and oxidation can be modeled in detail.
CFD aids in gaining a thorough grasp of how different fuels burn under varied operational and environmental conditions. Additionally, it aids combustion engineers in quickly determining the ideal air-fuel combination or stoichiometric ratio needed for successful combustion, resulting in the maximum usage of a fuel’s heating value and the least amount of pollutant generation. Additionally, it assists in cost-effectively optimising the operational parameter settings necessary for various operating situations, resulting in less fuel loss than when done via the trial-and-error method.
In order to achieve an effective burning process and increase the dependability of the combustion systems, it also aids in optimising the design of burners and other related air and fuel delivery systems.
In the area of coal combustion, we provide our assistance in modelling the process of coal combustion in any type of PC-fired boiler (Tangentially fired, wall-fired, and fluidized bed type boiler systems), providing a thorough evaluation of the combustion characteristics of the fuel used, the stoichiometric ratio necessary, the resulting temperature profile within the combustion chamber, and subsequent passes, as well as information about the by-product formations.
We provide our assistance in improving the design of burners and other related air and fuel delivery systems utilised to achieve an efficient burning process in the domain of combustion systems.

Liquid Fuel Combustion
Unlike the combustion of gaseous fuel, the combustion of liquid fuel is a multistage process that includes the phase transfer of the fuel prior to combustion. For improved optimisation of the combustion process and related phenomena, comprehensive analysis of the combustion of liquid fuels using CFD can be carried out. Along with helping to increase the dependability of the combustion system as a whole, it also aids in optimising the design of the fuel injection system, fuel supply system, and combustion air system related to the process of combustion.
We offer the following services in the area of liquid fuel combustion
- Detailed assessment of the process of combustion with various fuels and resulting thermal and chemical phenomena
- Detailed assessment of the spray process, including the vaporisation phenomenon with respect to the fuel injector Injector characteristics in relation to spray formation can also be thoroughly evaluated
- Optimization of fuel injection characteristics, including the injection pressure, flow rate, optimal air-fuel mixture ratio, and injection time requirements
- Optimization of combustion systems such as Burner components (nozzle diameter and other associated geometric features) and air-fuel supply systems to achieve an efficient burning process while improving the reliability of the combustion systems
- Detailed analysis of the thermal profile resulting from combustion within the combustion chambers and the resulting pollutant formation and its trend within the combustion chamber

Coal Conveyor
The main issues at a pulverised coal-based power plant’s crusher house are dust creation, coal loss due to dust, and heavy wear and tear on conveyor parts such as transfer chutes and conveyor belts. CFD aids in optimising the dust creation process, minimizing coal loss due to dust, and enhancing the dependability of coal conveyor parts utilised in the crushed house.
We offer the following services in the area of coal conveyor systems
- Optimization of dust suppression systems and their components (blower, fan, and dust filtering systems
- Optimal installation of dust suppression systems for effective and improved coal utilization
- Optimization of conveyor components (such as transfer chutes, conveyor belt speeds, and enclosures) to reduce the wear and tear resulting from coal transportation through flow optimisation of solid particles Identifying erosion-prone zones and providing suitable provisions to avoid any premature failure of components


Cold Air Velocity Test (CAVT)
burning coal Flyash erosion causes catastrophic tube failures in boilers. Flyash erosion occurs naturally when coal is burned, but it is sped up by isolated high-velocity zones that form because the boiler has a free flow path. By installing proper flow control devices in specific areas, erosion can be slowed down. The use of CFD analysis has been extremely crucial in giving optimal and cost-effective solutions in a shorter amount of time because it is a labour-intensive and time-consuming process.
We offer the following services in the area of Boiler Flow optimisation
- Detailed assessment of the localised velocity distribution pattern and identification of erosion-prone zones within the first and subsequent passes of the boiler, via in situ testing and CFD analysis
- Identify a suitable design and location for the installation of flow control arrangements to reduce or mitigate erosion in Boiler second and subsequent passes as per the required standard requirements

ID FAN Analysis
Power plants primarily use centrifugal and axial flow fans to supply combustion air and remove flue gas from the combustion chamber and into the chimney. The centrifugal fan is evolving in the direction of high efficiency and energy conservation with the increase of its application in the power sector. The new design approach aims to reduce the design period and enhance performance while being economically viable. The creation of innovative, effective fans for industrial applications relies heavily on CFD analysis, which is also proving to be a cost-effective tool in this industry. Using CFD techniques, any current design may be retrofitted for increased efficiency with little effort and expense.
We offer the following services for ID fans
- Performance assessment of a new and existing design
- Fan characteristic curve generation for various operating conditions
- Rotodynamic analysis is used to assess the structural and vibration characteristics of the fan
- Acoustic characteristics of the fan to ensure smoother and safer operating limits for new and existing designs


Pulverizers
We offer the following services for pulverizers
- Flow analysis within the pulverizers (Ball tube mills, Ball and race mills, and Bowl mill-type pulverizers)
- Flow distribution pattern of hot primary air and coal particle dispersion study
- Flow distribution between the mill outlets to assess the distribution of coal and air between burners
- Vane wheel assembly configuration optimisation to ensure less drag and better lift off coal particles
- Classifier position optimisation for the required flow configuration of the air/coal mixture

Clean and Dirty Air Flow Analysis
In order to supply the fuel needed to meet changing load needs, coal pulverizers are built to work at various speeds. Due to the critical role that air flow plays in combustion, it is crucial to ensure that each pulverizer receives an equal amount of air and that the air/coal combination is distributed through numerous nozzles at different firing heights of the boiler. In order to guarantee an equal flow of air or fuel through each air-coal discharge pipe from the pulverizer—required for efficient combustion—cold air flow tests (CAFT) and dirty air flow tests (DAFT) are being conducted.
We offer the following services
- Variable and fixed Orifice size, opening, and position optimisation to ensure the distribution of air/coal mixture through all burners meets the standard requirements
- Flow assessment to check the adequacy of existing mill configuration and layout to meet combustion requirements
- Velocity distribution and pressure drop prediction within the mill and coal pipe

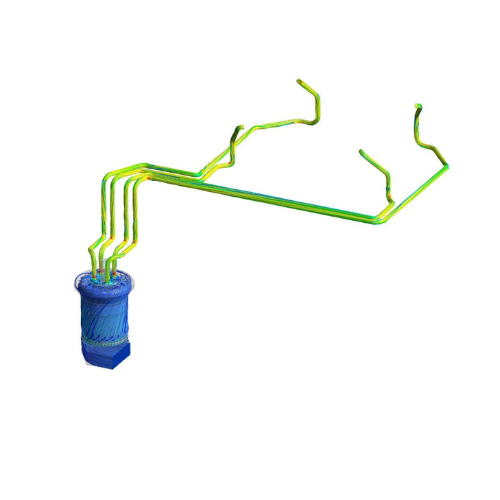
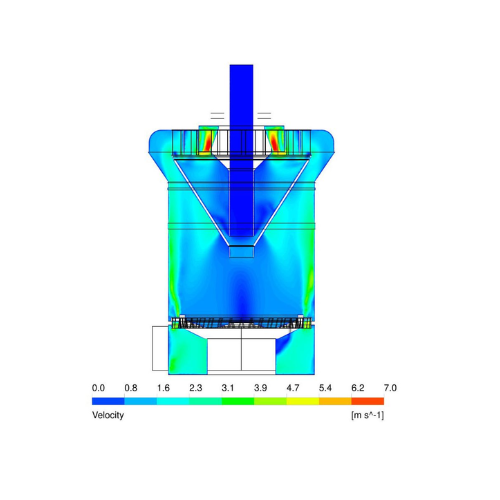